Sferolite APM 600
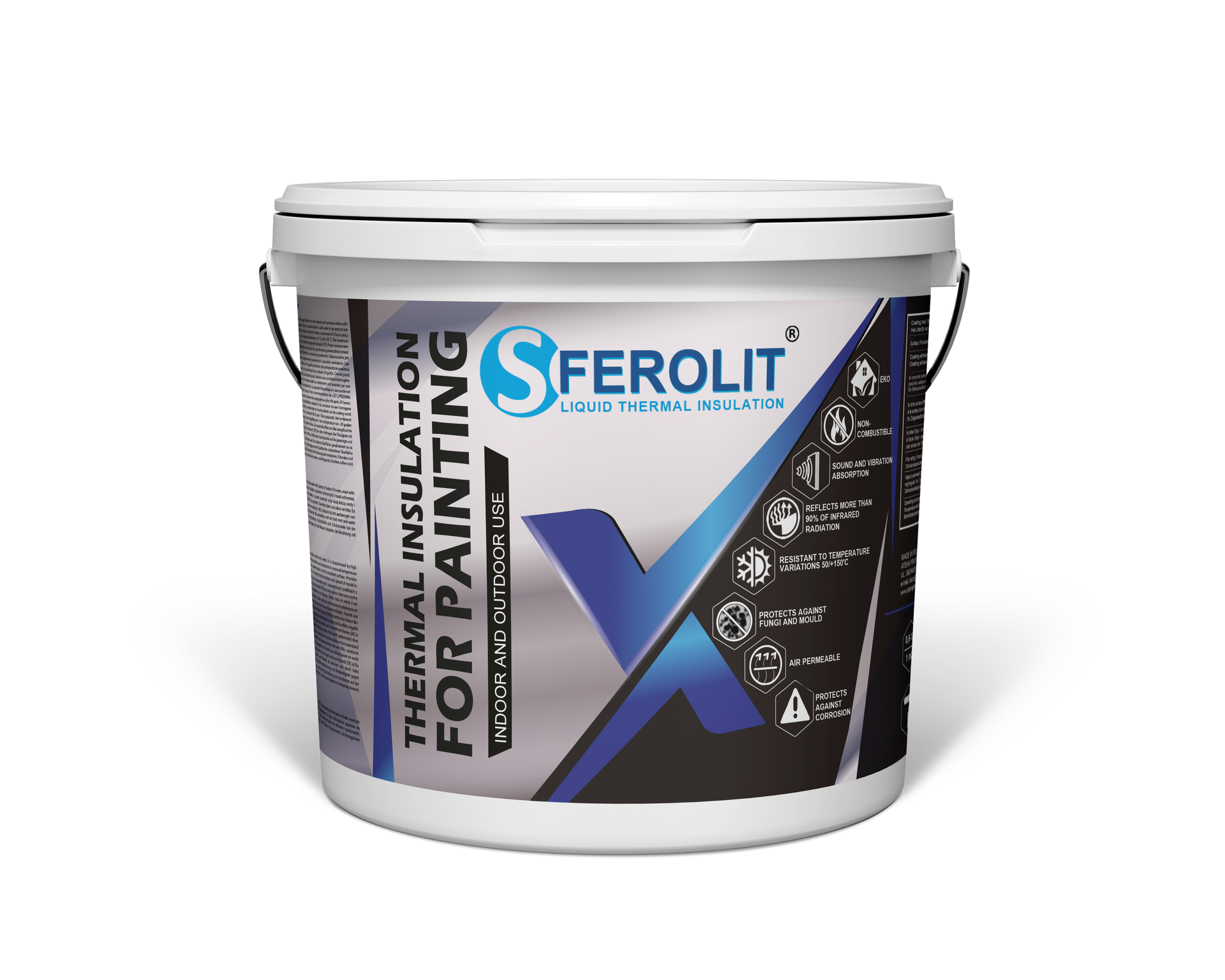
THERMAL INSULATION LIQUID COATING
TECHNICAL DATA SHEET
PRODUCT DESCRIPTION:
SFEROLIT® is a liquid ceramic coating renowned for its exceptional thermal and waterproofing properties, making it an ideal solution for heavy industry applications. This advanced coating incorporates a microceramic filler blended with acrylic copolymers, providing superior performance in demanding environments.
Designed to withstand extreme conditions, SFEROLIT serves as a highly effective antifungal, anti-corrosive, and thermal insulation coating for a wide range of industrial needs. It offers reliable protection for external and internal structures, including enclosures, machinery, roofing, tanks, furnaces, boilers, piping, ventilation, and air-conditioning systems.
The insulating properties of SFEROLIT are based on the incorporation of millions of vacuum hollow particles. These particles form a robust membrane upon application and drying, effectively reducing heat loss by up to 60%. Additionally, SFEROLIT is impervious to water while allowing for proper breathability of the coated surface.
Thanks to its vapor permeability, SFEROLIT enables intensive air exchange, saving an additional 7-9% of heat and providing excellent resistance against fungi, mold, corrosion, and other environmental challenges. Its remarkable flexibility allows for expansion by a quarter without compromising adhesion, ensuring long-lasting performance in high-stress environments.
With the ability to withstand up to 380 ml of water per hour and rapid drying capabilities, SFEROLIT excels in heavy industry applications. It is particularly well-suited for use in furnaces, where it provides efficient thermal insulation and robust protection against the extreme temperatures typically encountered at operating temperatures from -40°С to+600°C.
Choose SFEROLIT for your heavy industry needs, and experience the unmatched performance and durability of this cutting-edge liquid ceramic coating.
ADVANTAGES
✓ Dew point - minimises the effects of condensation
✓ Operating temperature between -40°C and +600°C
✓ Computational lambda 0.0012 W/mK
✓ Anti - corrosion protection
✓ Non-flammable - flammability class B1
✓ High adhesion
✓ Vapor permeable
✓ Protects against moisture
✓ Ecological
✓ Water-based - no explosion hazard during application and storage
✓ Increases safety of tanks against overheating and explosion
✓ Antistatic qualities
✓ Protection against mould and fungi
✓ Protects against weather conditions
✓ Increases sound insulation - min. 10%
✓ Absorbs vibrations
✓ Increases energy efficiency
✓ Reduces energy consumption costs
✓ Highly durable
✓ Increases displacement in sea transportation
✓ Harmless to health
✓ No waste (high insulation savings)
✓ Application does not harm insects
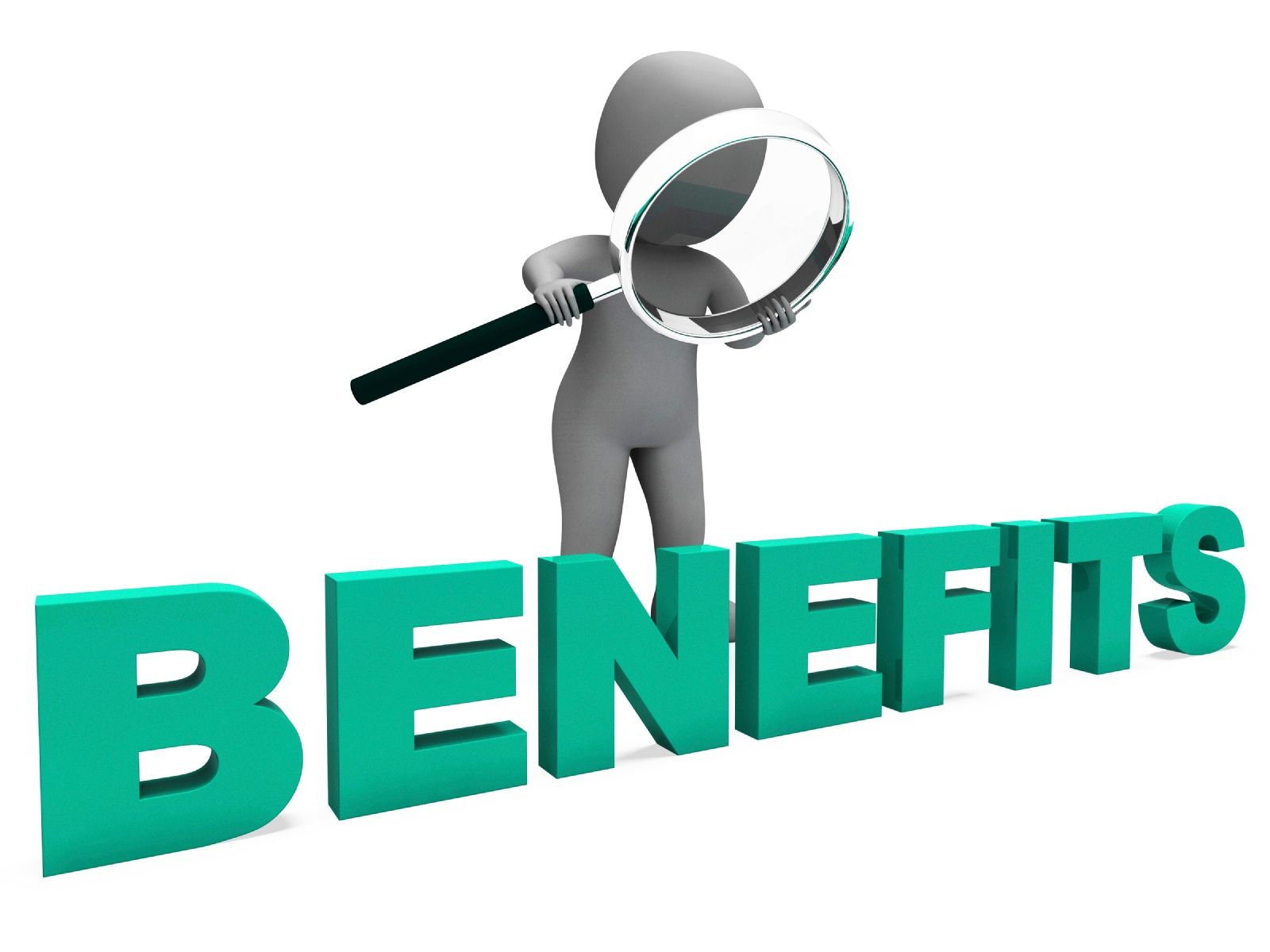
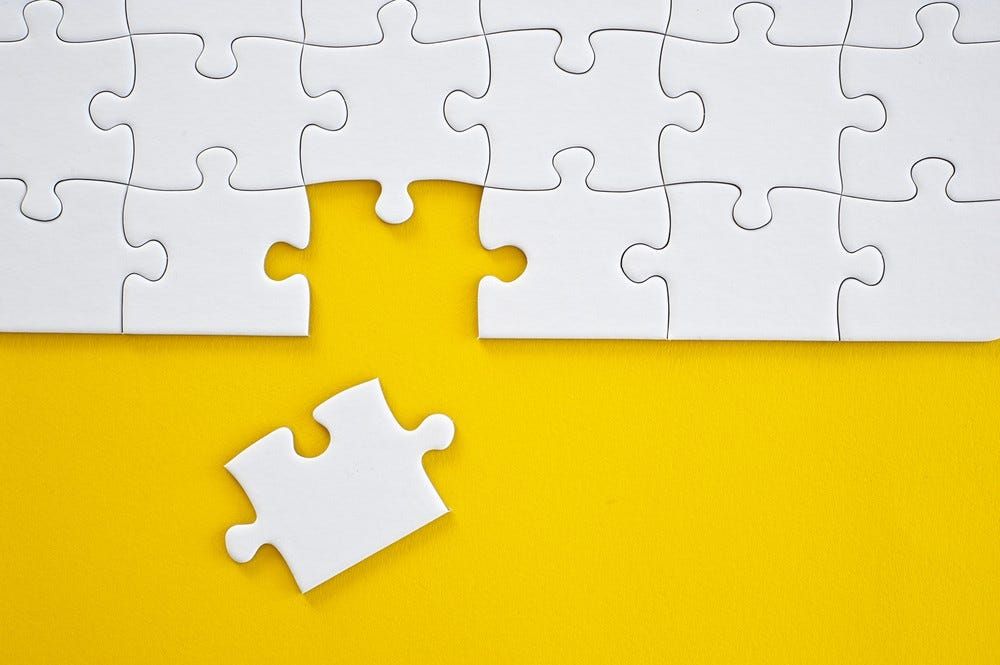
SUITABILITY
✓ in the energy, petrochemical and industrial sectors for thermal-acoustic and anticorrosive insulation of metal surfaces: district heating pipes, boilers, quenching furnaces, fuel tanks, machinery and equipment generating extremely high and low temperatures
Specification
The physical state
Colour
Smell
Boiling point, initial boiling point and boiling range
Flash point
Decomposition temperature
Liquid
White
Faint
approx. 100°C.
Not applicable
Not applicable
KEY FEATURES
Reaction to fire - characteristics according to Euroclass
Pull-off adhesion (concrete, brick, steel)
Water vapour permeability
Capillary absorption and water permeability
Hygiene Certificate
Density
Operating temperatures
Thermal conductivity
TSR %
Emissivity
SRI
PERFORMANCE
Reaction to fire: B-s1.d0
Average: 1.6 N / mm² (cohesive fracture at the base)
9.4 g / m² x d
Average: 0.20 kg / (m² x hº. ⁵)
The product was assessed positively for hygiene
0.45 - 0.55 g / cm3
from -50 ° C to + 150 ° C
λ 0,0012 W/mK
89,43
0,98
110
HARMONISED STANDARD
EN 1504-2:2004
-
ISO 22969-2019-7, ASTM E903
-
ASTM E1980- 11(2019)
Product Information
CAN BE APPLIED TO:
Concrete, ceramics (brick, brick-block and other building materials), metal & stainless steel.
DRYING TIME:
The applied layer, up to a thickness of 1mm, dries within 3 and up to 24 hours. The drying time of the applied layer with thickness of 1mm at the temperature of + 20˚С and relative humidity of up to 60% - 3 hours. Full curing depends on the ambient temperature, humidity, ventilation and the thickness of the applied layer and lasts from 0.5 up to max. 24 hours. Force drying is not recommended.
TYPE OF MATERIAL:
Water-based, non-toxic, non-flammable (wet and dry).
COLOR:
White
HEALTH AND SAFETY:
The compound is non-toxic and non-flammable. Dry coating waste can be disposed of as no risk. Please see the separate safety data sheet.
LAYER COVERAGE:
The intended coverage is approximately 1L per 1m2 with a single layer of between 0.8 and 1.2mm thickness (wet layer).The coverage depends on the requirements of the surface, the structure and the expected insulation parameters. The maximum recommended thickness: four layers of approx. 4mm (4L / m2 ).
COATING REPAIRS:
if the coating gets mechanically damaged, repair the surface by rubbing the surface with sandpaper, prime the surface with a deep primer, apply a fresh layer and allow it to dry and fully harden.
STORAGE:
Shelf life: 12 months. After the durability period, it is subject to re-inspection. Should be protected from frost throughout the entire storage period. Should be stored between 5°C and 25°C. and protected from sunlight. Containers should be tightly closed. Open or partially filled containers - scum formation may occur. In such a case, the top layer should be removed before use. It is recommended to cover the remaining amount in the bucket, to protect it from air access and water evaporation from the bucket. Do not allow the fluid to freeze!
COATING REPAIRS:
if the coating gets mechanically damaged, repair the surface by rubbing the surface with sandpaper, prime the surface with a deep primer, apply a fresh layer and allow it to dry and fully harden.
REMOVAL:
The wet layer can be easily removed with water or with a pressure hose. After drying, the coating is difficult to remove from surfaces and tools.
CLEANING:
Clean rollers, guns and other equipment with water immediately after use.
PACKAGING:
Plastic buckets with a capacity of 20 L
APPLICATION INFORMATION AND RECOMMENDATIONS
for detailed instructions see application instructions and use a wet film gauge to ensure minimum and maximum wet film thickness is achieved.
Before use, the contents of the container should be thoroughly mixed at medium speed until a homogeneous consistency is obtained.
Before use, the surface must be primed with a deeply TECHNICAL DATA SHEET Valid from: February 4, 2023 penetrating primer (in case of building materials), and in the case of application on steel, thoroughly remove the signs of rust mechanically and degrease the surface.
Sferolite can be then applied to the cleaned surface with a brush, a roller or a paint gun. It is allowed to add water in an amount not exceeding 70ml per 1 litre of the preparation.
The minimum wet film thickness is 0.8mm, the maximum is 1.2mm [wet film]. Do not apply in wet or frosty conditions (apply at an air temperature of +5 to + 35˚С), protect against rainfall until it is completely dry and avoid applying when rainfall is predicted within 24 hours.
The drying time of the applied layer with a layer thickness of up to 1mm at a temperature of + 20˚С and a relative humidity of up to 60% - 3 hours.
Spray application:
- Preparation for application: tools for spray painting should be thoroughly rinsed with clean water. They must be completely clean;
- The surface should be clean from dirt, primed / degreased;
- Apply with a spray gun to obtain a minimum thickness of 0.8mm and a maximum of 1.2mm [wet film];
- When applying with an air spray gun, the mass should be diluted with water up to 7% of the total mass of the material;
- The application should be carried out in circular movements and subsequent layers should be applied after the previous layer has dried and cured completely. The film applied by spraying will be more homogeneous.
PERSONAL PROTECTION / HEALTH & SAFETY
During application, it is recommended to use a protective mask, protective gloves (prevention of e.g. an allergic reaction), protective glasses (in particular when applying with a pressure gun), painting suit to avoid stains on shoes and clothes, hearing protection, headphones when using a compressor during spray painting.
PRECAUTIONS:
Observe the recommendations given in the safety data sheet. This data sheet does not contain information on the safety of the product. Before using the product, read the safety data sheet and the labels on the packaging in order to obtain information about the safe use and health and physical hazards. Dispose of in accordance with applicable legislation. Keep out of the reach of children. Notes for the client: The above information is accurate and to the best of our knowledge, based on reliable research and practical experience.
The specified properties are provided for guidance only and do not constitute guaranteed product properties. The customer should test the product for specific applications to be sure that it has the expected properties and provides the required operational performance.